by Claudia Engel, Fraunhofer-Gesellschaft
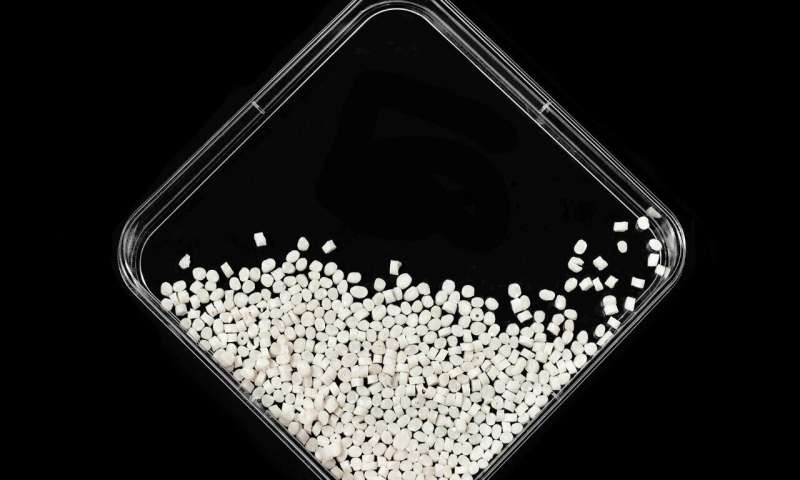
Compounded and granulated polyhydroxybutyrate (PHB). Credit: Fraunhofer-Gesellschaft
A new type of plastic made of reclaimed waste readily degrades in less than a year. The substance that will soon serve to manufacture and break down mainly disposable products in an ecofriendly way goes by the name of polyhydroxybutyrate. This innovative material can be produced on an industrial scale in a new process developed by the Fraunhofer Institute for Production Systems and Design Technology IPK and its partners.
Everyday life devoid of plastics—that would be hard to imagine. They figure prominently in packaging and consumer goods, and are indispensable to industry applications such as automotive and medical engineering. Reuse and recycling of plastics from fossil resources is hardly common practice. On top of that, they degrade at a glacial pace and pollute the environment for a long time to come. The great patches of plastic waste floating on our oceans attest to their power to pollute. Plastic bottles and bags despoil beaches and, in many places, entire stretches of land.
The Bioeconomy International research initiative
The need for global recycling strategies is urgent, given plastics' heavy use all over the world. More and more governments are resorting to bans to curb the swelling tide of plastic waste. A viable option to replace fossil-based plastics on a large scale has yet to be found. This is why the German Federal Ministry of Education and Research (BMBF) launched the "Bioökonomie International" (Bioeconomy International) research initiative in close cooperation with Fraunhofer IPK, the Department of Bioprocess Technology of the Technical University of Berlin, regional industrial partners and international research partners from Malaysia, Columbia and the U.S.. These researchers are developing a method of manufacturing polymers without drawing on premium resources such as mineral, palm and rapeseed oils, the production of which is very detrimental to the environment.
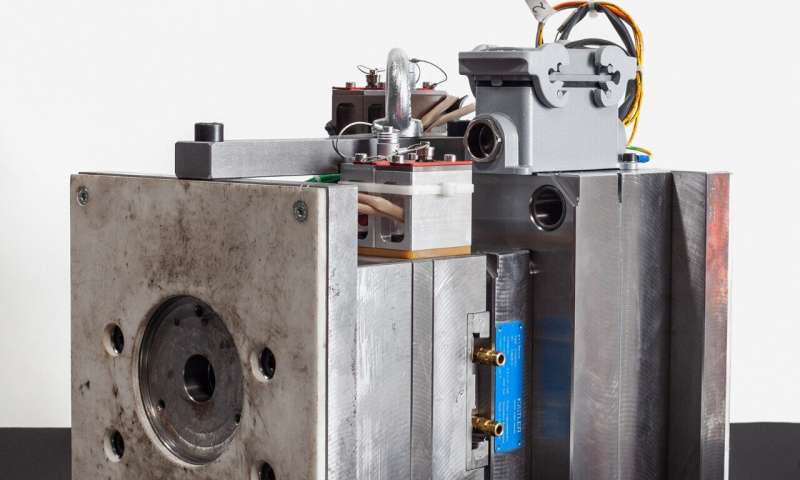
A new type of plastic made of reclaimed waste readily degrades in less than a year. The substance that will soon serve to manufacture and break down mainly disposable products in an ecofriendly way goes by the name of polyhydroxybutyrate. This innovative material can be produced on an industrial scale in a new process developed by the Fraunhofer Institute for Production Systems and Design Technology IPK and its partners.
Everyday life devoid of plastics—that would be hard to imagine. They figure prominently in packaging and consumer goods, and are indispensable to industry applications such as automotive and medical engineering. Reuse and recycling of plastics from fossil resources is hardly common practice. On top of that, they degrade at a glacial pace and pollute the environment for a long time to come. The great patches of plastic waste floating on our oceans attest to their power to pollute. Plastic bottles and bags despoil beaches and, in many places, entire stretches of land.
The Bioeconomy International research initiative
The need for global recycling strategies is urgent, given plastics' heavy use all over the world. More and more governments are resorting to bans to curb the swelling tide of plastic waste. A viable option to replace fossil-based plastics on a large scale has yet to be found. This is why the German Federal Ministry of Education and Research (BMBF) launched the "Bioökonomie International" (Bioeconomy International) research initiative in close cooperation with Fraunhofer IPK, the Department of Bioprocess Technology of the Technical University of Berlin, regional industrial partners and international research partners from Malaysia, Columbia and the U.S.. These researchers are developing a method of manufacturing polymers without drawing on premium resources such as mineral, palm and rapeseed oils, the production of which is very detrimental to the environment.
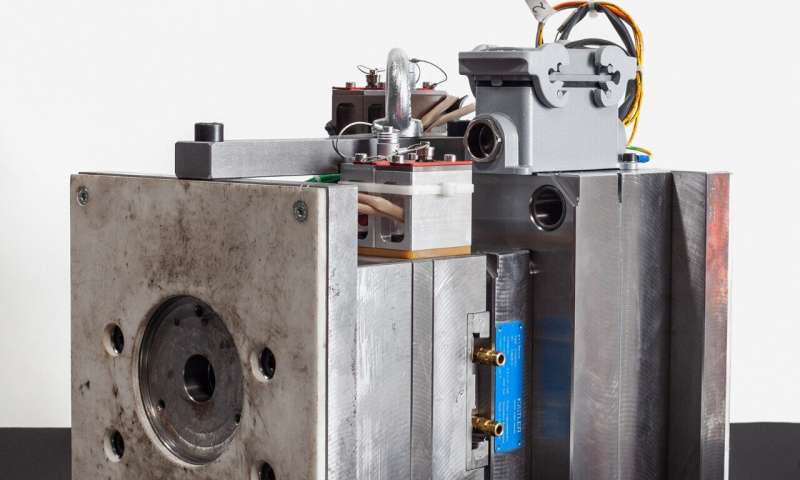
The Fraunhofer IPK team developed this injection molding tool to replicate prototype components made of polyhydroxybutyrate. Credit: Fraunhofer-Gesellschaft
A new plastic much like polypropylene
This new process turn industrial leftovers such as waste fats that contain a lot of mineral residue into polyhydroxybutyrate (PHB). Microorganisms can metabolize these residues in special fermentation processes. They deposit the PHB in their cells to store energy. "Once the plastic has been dissolved from the cell, it is still not ready for industrial use, because the hardening process takes far too long," says Christoph Hein, head of the Microproduction Technology department at Fraunhofer IPK. The raw material has to be mixed with chemical additives downstream in post-production stages. For example, the research team adjusted the plasticizing and processing parameters to trim the recrystallization time to fit the timing of industrial processing. The resultung biopolymer's properties resemble those of polypropylene. But unlike PP, this plastic degrades fully in six to twelve months.
In this method of producing plastic, microorganisms synthesize the entire polymer in a biotechnical process. "To this end, we convert biogenic residues such as waste fats into polyesters that can be put to technical use," says Hein. The researcher and his team opted for microorganisms, genetically modified with molecular methods, to serve as biocatalysts. With the help of chemical purification processes and an extensively optimized material, they have been able to develop a novel family of materials that satisfy the demands of technical plastics.
No petroleum-based synthetic components needed
The new process not only dispenses with petroleum-based synthetic components altogether; it also enables green plastic alternatives. Naturally occurring microorganisms can break down these newly developed plastics, so they need not be subjected to the special conditions that serve to degrade matter in industrial composting plants. They offer an ecofriendly alternative to making and degrading single-use products and other disposable items.
The process also lends itself to producing high-quality plastic parts for certain technical applications and periods of use. The specifications for this sort of product are more demanding. They may have to exhibit specific geometric tolerances and surface qualities or be reproducible with great precision. The researchers developed highly specialized replication processes to meet these requirements.
Explore furtherA new method for recycling plastics together
A new plastic much like polypropylene
This new process turn industrial leftovers such as waste fats that contain a lot of mineral residue into polyhydroxybutyrate (PHB). Microorganisms can metabolize these residues in special fermentation processes. They deposit the PHB in their cells to store energy. "Once the plastic has been dissolved from the cell, it is still not ready for industrial use, because the hardening process takes far too long," says Christoph Hein, head of the Microproduction Technology department at Fraunhofer IPK. The raw material has to be mixed with chemical additives downstream in post-production stages. For example, the research team adjusted the plasticizing and processing parameters to trim the recrystallization time to fit the timing of industrial processing. The resultung biopolymer's properties resemble those of polypropylene. But unlike PP, this plastic degrades fully in six to twelve months.
In this method of producing plastic, microorganisms synthesize the entire polymer in a biotechnical process. "To this end, we convert biogenic residues such as waste fats into polyesters that can be put to technical use," says Hein. The researcher and his team opted for microorganisms, genetically modified with molecular methods, to serve as biocatalysts. With the help of chemical purification processes and an extensively optimized material, they have been able to develop a novel family of materials that satisfy the demands of technical plastics.
No petroleum-based synthetic components needed
The new process not only dispenses with petroleum-based synthetic components altogether; it also enables green plastic alternatives. Naturally occurring microorganisms can break down these newly developed plastics, so they need not be subjected to the special conditions that serve to degrade matter in industrial composting plants. They offer an ecofriendly alternative to making and degrading single-use products and other disposable items.
The process also lends itself to producing high-quality plastic parts for certain technical applications and periods of use. The specifications for this sort of product are more demanding. They may have to exhibit specific geometric tolerances and surface qualities or be reproducible with great precision. The researchers developed highly specialized replication processes to meet these requirements.
Explore furtherA new method for recycling plastics together
Provided by Fraunhofer-Gesellschaft
Transforming waste into bio-based chemicals
by Emily Scott, Lawrence Berkeley National Laboratory
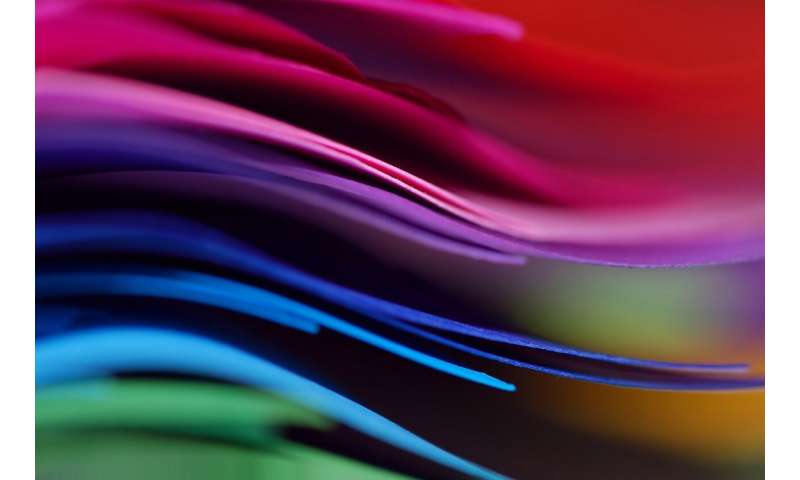
Credit: Pixabay/CC0 Public Domain
Researchers at Berkeley Lab have transformed lignin, a waste product of the paper industry, into a precursor for a useful chemical with a wide range of potential applications.
Lignin is a complex material found in plant cell walls that is notoriously difficult to break down and turn into something useful. Typically, lignin is burned for energy, but scientists are focusing on ways to repurpose it.
In a recent study, researchers demonstrated their ability to convert lignin into a chemical compound that is a building block of bio-based ionic liquids. The research was a collaboration between the Advanced Biofuels and Bioproducts Process Development Unit, the Joint BioEnergy Institute (both established by the Department of Energy and based at Berkeley Lab), and the Queens University of Charlotte.
Ionic liquids are powerful solvents/catalysts used in many important industrial processes, including the production of sustainable biofuels and biopolymers. However, traditional ionic liquids are petroleum-based and costly. Bio-based ionic liquids made with lignin, an inexpensive organic waste product, would be cheaper and more environmentally friendly.
"This research brings us one step closer to creating bio-based ionic liquids," said Ning Sun, the study's co-corresponding author. "Now we just need to optimize and scale up the technology."
According to Sun, bio-based ionic liquids also have a broad range of potential uses outside of industry. "We now have the platform to synthesize bio-based ionic liquids with different structures that have different applications, such as antivirals," Sun said.
Explore further Making biodiesel with green solvents
Researchers at Berkeley Lab have transformed lignin, a waste product of the paper industry, into a precursor for a useful chemical with a wide range of potential applications.
Lignin is a complex material found in plant cell walls that is notoriously difficult to break down and turn into something useful. Typically, lignin is burned for energy, but scientists are focusing on ways to repurpose it.
In a recent study, researchers demonstrated their ability to convert lignin into a chemical compound that is a building block of bio-based ionic liquids. The research was a collaboration between the Advanced Biofuels and Bioproducts Process Development Unit, the Joint BioEnergy Institute (both established by the Department of Energy and based at Berkeley Lab), and the Queens University of Charlotte.
Ionic liquids are powerful solvents/catalysts used in many important industrial processes, including the production of sustainable biofuels and biopolymers. However, traditional ionic liquids are petroleum-based and costly. Bio-based ionic liquids made with lignin, an inexpensive organic waste product, would be cheaper and more environmentally friendly.
"This research brings us one step closer to creating bio-based ionic liquids," said Ning Sun, the study's co-corresponding author. "Now we just need to optimize and scale up the technology."
According to Sun, bio-based ionic liquids also have a broad range of potential uses outside of industry. "We now have the platform to synthesize bio-based ionic liquids with different structures that have different applications, such as antivirals," Sun said.
Explore further Making biodiesel with green solvents
More information: Shihong Liu et al. Statistical design of experiments for production and purification of vanillin and aminophenols from commercial lignin, Green Chemistry (2020). DOI: 10.1039/D0GC01234C
Journal information: Green Chemistry
Provided by Lawrence Berkeley National Laboratory
Bacteria fed on a customized diet produce biodegradable polymers for alternative packaging in the cosmetics industry
by Claudia Vorbeck, Fraunhofer-Gesellschaft
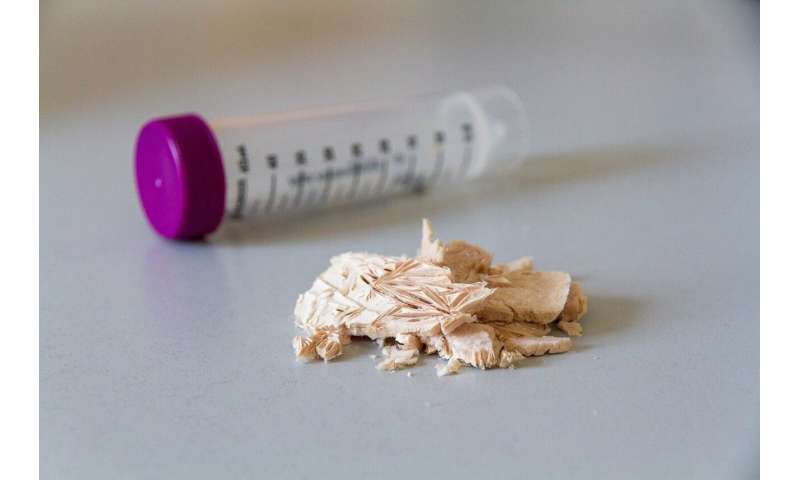
Provided by Lawrence Berkeley National Laboratory
Bacteria fed on a customized diet produce biodegradable polymers for alternative packaging in the cosmetics industry
by Claudia Vorbeck, Fraunhofer-Gesellschaft
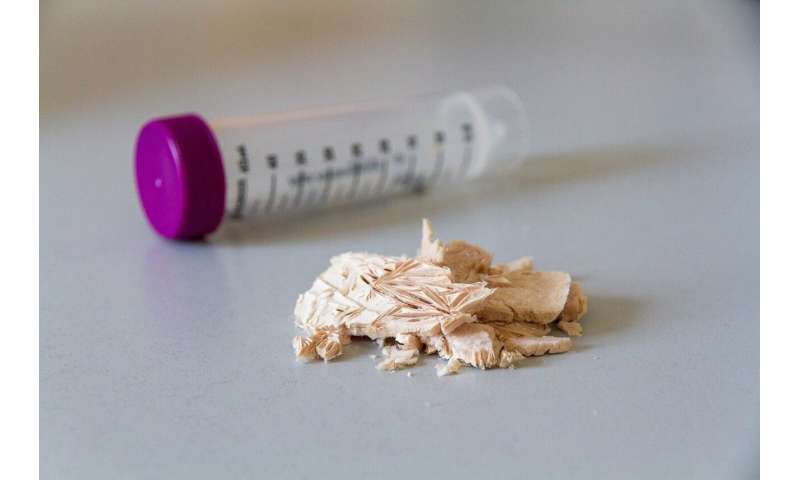
Freeze-dried bacteria (Cupriavidus necator) before cell disruption. Credit: Fraunhofer-Gesellschaft
Germany generates around 38 kilograms of plastic waste per capita each year. In a joint project with the University of Stuttgart and LCS Life Cycle Simulation, researchers from the Fraunhofer Institute for Interfacial Engineering and Biotechnology IGB and the Fraunhofer Institute for Process Engineering and Packaging IVV are now working to establish a holistic concept for the sustainable use of biologically degradable packaging materials in the cosmetics industry. The project is focusing on polyhydroxyalkanoates (PHAs), which have similar properties to conventional plastics but are produced from microorganisms and without the use of fossil-based raw materials.
To date, the bacteria in Dr. Susanne Zibek's lab at Fraunhofer IGB in Stuttgart have been fed on a whole variety of waste materials, ranging from wood waste and oil and sugar residues to glycerol from biodiesel production. Each of these carbon-based feed sources causes the bacteria to produce specific intracellular storage granules. These so-called polyhydroxyalkanoates (PHAs) are the focus of SusPackaging, a research project that is being conducted in cooperation with Fraunhofer IVV in Freising, the University of Stuttgart and LCS Life Cycle Simulation, which is located in the town of Backnang. Researchers from Fraunhofer IGB are seeking to create biologically based, biodegradable polymers as a replacement for plastic packaging in the cosmetics industry. What sets the project apart is its attempt to establish a wholly green value chain. As Dr. Ana Lucía Vásquez-Caicedo from Fraunhofer IGB explains, a holistic concept with a focus on sustainability is new: "A lot of studies concentrate on individual aspects, but it's rare to see a consideration of the entire process chain all the way up to an evaluation of the quality of materials."
The process begins with cultivation of the bacteria. Dr. Susanne Zibek, group manager of the Food Processing Technology Group, and her colleague Dr. Thomas Hahn are investigating how specific microorganisms can be used to produce different PHAs with different structures, and how the choice of feed influences their characteristics. "Basically, we're trying to create new structural variants, so that we can then see whether the polymer produced is suitable as a packaging material," Zibek explains. The working group has support from researchers at the University of Stuttgart, who are taking a closer look at various characteristics of the microorganisms, including the extent to which they can adapt to toxic substances that might be contained in the natural feed sources.
Replacing harmful solvents with pressure change technology
Before the PHAs can be processed and tested, they must first be extracted from the microorganisms. This is the specialist field of Vásquez-Caicedo, group manager of the Food Processing Technology Group at Fraunhofer IGB. As a rule, this so-called purification process uses solvents such as chloroform. However, as she explains, the aim is to move away from environmentally harmful solvents. Instead, she has developed a purely mechanical/physical method of cell disruption. Known as pressure change technology (PCT), this involves the addition of a process gas to the fermentation broth containing the microorganisms. The broth is then pressurized, with the result that the gas penetrates the cytoplasm of the cells. A rapid lowering of pressure in the broth destroys the cells and releases the PHA.
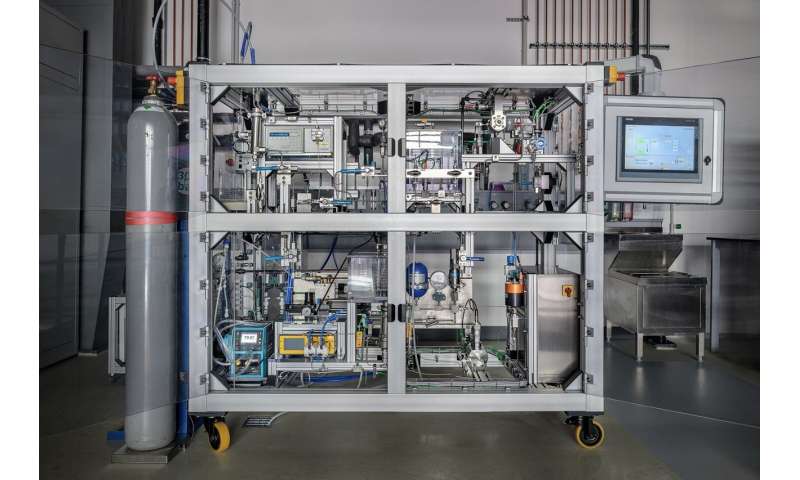
Germany generates around 38 kilograms of plastic waste per capita each year. In a joint project with the University of Stuttgart and LCS Life Cycle Simulation, researchers from the Fraunhofer Institute for Interfacial Engineering and Biotechnology IGB and the Fraunhofer Institute for Process Engineering and Packaging IVV are now working to establish a holistic concept for the sustainable use of biologically degradable packaging materials in the cosmetics industry. The project is focusing on polyhydroxyalkanoates (PHAs), which have similar properties to conventional plastics but are produced from microorganisms and without the use of fossil-based raw materials.
To date, the bacteria in Dr. Susanne Zibek's lab at Fraunhofer IGB in Stuttgart have been fed on a whole variety of waste materials, ranging from wood waste and oil and sugar residues to glycerol from biodiesel production. Each of these carbon-based feed sources causes the bacteria to produce specific intracellular storage granules. These so-called polyhydroxyalkanoates (PHAs) are the focus of SusPackaging, a research project that is being conducted in cooperation with Fraunhofer IVV in Freising, the University of Stuttgart and LCS Life Cycle Simulation, which is located in the town of Backnang. Researchers from Fraunhofer IGB are seeking to create biologically based, biodegradable polymers as a replacement for plastic packaging in the cosmetics industry. What sets the project apart is its attempt to establish a wholly green value chain. As Dr. Ana Lucía Vásquez-Caicedo from Fraunhofer IGB explains, a holistic concept with a focus on sustainability is new: "A lot of studies concentrate on individual aspects, but it's rare to see a consideration of the entire process chain all the way up to an evaluation of the quality of materials."
The process begins with cultivation of the bacteria. Dr. Susanne Zibek, group manager of the Food Processing Technology Group, and her colleague Dr. Thomas Hahn are investigating how specific microorganisms can be used to produce different PHAs with different structures, and how the choice of feed influences their characteristics. "Basically, we're trying to create new structural variants, so that we can then see whether the polymer produced is suitable as a packaging material," Zibek explains. The working group has support from researchers at the University of Stuttgart, who are taking a closer look at various characteristics of the microorganisms, including the extent to which they can adapt to toxic substances that might be contained in the natural feed sources.
Replacing harmful solvents with pressure change technology
Before the PHAs can be processed and tested, they must first be extracted from the microorganisms. This is the specialist field of Vásquez-Caicedo, group manager of the Food Processing Technology Group at Fraunhofer IGB. As a rule, this so-called purification process uses solvents such as chloroform. However, as she explains, the aim is to move away from environmentally harmful solvents. Instead, she has developed a purely mechanical/physical method of cell disruption. Known as pressure change technology (PCT), this involves the addition of a process gas to the fermentation broth containing the microorganisms. The broth is then pressurized, with the result that the gas penetrates the cytoplasm of the cells. A rapid lowering of pressure in the broth destroys the cells and releases the PHA.
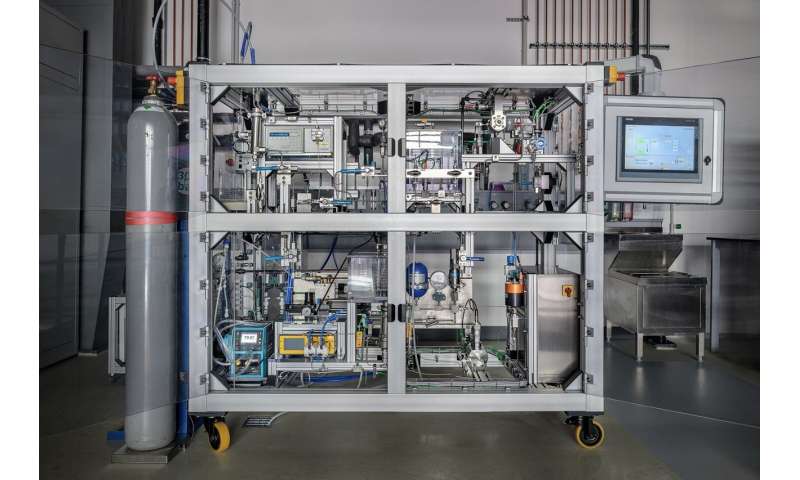
Lab equipment for cell disruption and extraction of functional materials at Fraunhofer IGB. Credit: Fraunhofer-Gesellschaft
Following purification, the PHA is sent in the form of a white powder to Fraunhofer IVV in Freising. Here, it is turned first into granules and then into a polymer film. Initial testing on small sheets of this polymer has examined material characteristics such as thermal stability, plasticity and various barrier properties—essential if future packaging is to provide cosmetic ingredients with, for example, effective protection against desiccation.
Dr. Cornelia Stramm from Fraunhofer IVV is happy with the results so far: "In terms of their mechanical properties, some PHA types are still proving somewhat difficult to process. We need to make a few adjustments there. But in terms of their barrier properties, PHAs show great potential compared to other biopolymers." At the end of each testing cycle, she sends the results back to Stuttgart along with recommendations for further action, and then the process begins again.
Based on this feedback from Fraunhofer IVV, Zibek's working group at Fraunhofer IGB has modified its feed strategy. The bacteria are now given an additional cosubstrate, which increases the PHA's valerate content, thereby making the end product more pliable.
Further enhancement with every feedback loop
While volumes are still very low and production takes a lot of time, the process is steadily improving with each feedback loop.
Once the various steps have been finalized, a life cycle analysis conducted by external project partner LCS Life Cycle Simulation will evaluate the energy efficiency and sustainability of the entire process in order to compare it with existing processes. All three researchers from Fraunhofer see big potential for PHAs. In the future, particularly for small items of disposable packaging, they could offer a genuine alternative to conventional petroleum-based plastics.
Explore further
Following purification, the PHA is sent in the form of a white powder to Fraunhofer IVV in Freising. Here, it is turned first into granules and then into a polymer film. Initial testing on small sheets of this polymer has examined material characteristics such as thermal stability, plasticity and various barrier properties—essential if future packaging is to provide cosmetic ingredients with, for example, effective protection against desiccation.
Dr. Cornelia Stramm from Fraunhofer IVV is happy with the results so far: "In terms of their mechanical properties, some PHA types are still proving somewhat difficult to process. We need to make a few adjustments there. But in terms of their barrier properties, PHAs show great potential compared to other biopolymers." At the end of each testing cycle, she sends the results back to Stuttgart along with recommendations for further action, and then the process begins again.
Based on this feedback from Fraunhofer IVV, Zibek's working group at Fraunhofer IGB has modified its feed strategy. The bacteria are now given an additional cosubstrate, which increases the PHA's valerate content, thereby making the end product more pliable.
Further enhancement with every feedback loop
While volumes are still very low and production takes a lot of time, the process is steadily improving with each feedback loop.
Once the various steps have been finalized, a life cycle analysis conducted by external project partner LCS Life Cycle Simulation will evaluate the energy efficiency and sustainability of the entire process in order to compare it with existing processes. All three researchers from Fraunhofer see big potential for PHAs. In the future, particularly for small items of disposable packaging, they could offer a genuine alternative to conventional petroleum-based plastics.
Explore further
Provided by Fraunhofer-Gesellschaft
No comments:
Post a Comment