Eight Ports in the British Isles Get Electric Ship Charging Stations
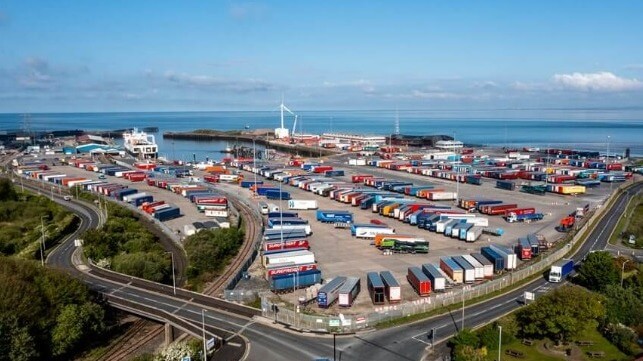
The UK’s second largest port operator, Peel Ports Group, has announced plans to establish the first green shipping corridor between the UK and Ireland. This is part of a artnership between the port operator and the marine tech company NatPower Marine. The collaboration will see NatPower Marine develop the UK’s first commercial electric charging network to support electric propulsion and cold ironing (shore power).
The charging infrastructure will require an estimated investment of $127 million and will be delivered across all eight UK and Ireland ports operated by Peel Ports Group. The masterplan of the infrastructure also includes electric car, van and truck chargers for commercial electric vehicles passing through the ports.
This investment in the UK is part of a $3.8 billion global charging network, planed by NatPower Marine for 120 port locations worldwide by 2030.
“NatPower Marine is investing to deploy the largest global network of charging ports to help resolve the ‘chicken and egg conundrum’ facing this industry: shipping lines cannot electrify vessels if port charging infrastructure is not available, and ports are unable to raise capital for charging infrastructure without certainty of demand from shipping lines,” said Stefano Sommadossi, CEO NatPower Marine.
With over 3,000 vessels crossing the Irish Sea every year, emitting 230,000 tons of CO2 and 20,000 tons of nitrous oxide, this partnership may drastically reduce emissions.
The first Irish Sea routes identified in the project proposals include Belfast-Heysham and Dublin-Birkenhead. The small Port of Heysham in Lancashire is on track to become the UK’s first net zero port, according to Peel Ports, and the charging infrastructure will support this goal. Currently, the port is leading in reduction of carbon emissions of its landside plant, equipment and vehicles by up to 90 percent. The port claims that all its vehicles, plant equipment, forklift trucks and ancillary equipment are now operating on either electricity or biofuels.
“The proposals presented as part of this partnership are potentially game-changing, and fully support our ambitions to become a net-zero port operator by 2040,” said Claudio Veritiero, CEO of Peel Ports Group.
In the past two years, the UK government has significantly invested in green shipping corridors, an initiative the UK led as part of the Clydebank Declaration during COP 26 in November 2021. Last month, the UK government launched the fifth round of Clean Maritime Demonstration Competition (CMDC 5), with funding of over $900,000 available for start-ups looking to establish green shipping routes to and from the UK.
Putting Methanol Through its "Paces," With a Focus on Safety
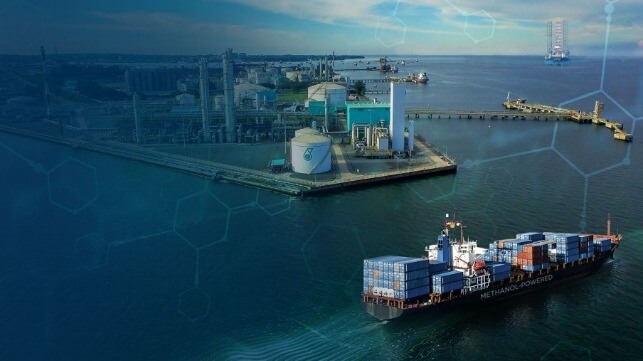
With more than 90% of global GDP now covered by a net zero target, the growing consensus to tackle climate change is matched only by a deepening understanding of the immensity of the challenge. For the shipping industry, there’s a real urgency to reverse the 20% emissions growth of the last decade and begin the essential but expensive task of decarbonizing the global fleet, 98.8% of which, according to a 2023 report from UNCTAD, still runs on fossil fuels.
The first challenge is to overcome the huge inertia of an aging fleet, with an average ship age of 22.2 years. With over half the global fleet older than 15 years, many ships are either too old to retrofit or too young to scrap. Over time, the replacement cycle will change the fleet’s emissions profile, as shipowners place orders for newbuilds that can run on cleaner fuels such as LNG, ammonia and methanol.
The clock is now ticking to accelerate that pace of change, particularly as the IMO’s enhanced GHG strategy for 2030 includes stricter targets to cut the carbon intensity of international shipping by 40%. Shipowners must act soon to transition their fleets because without clear investment signals the availability of candidate fuels will lag demand, creating further hesitancy and potentially derailing the transition.
Any new fuel, however, must be put through its PACES to meet the industry’s expectations on Performance, Availability, Cost, Emissions and Safety. Here, methanol has a head start because in terms of performance it’s already a proven fuel, with methanol storage available in over 100 ports around the world. Its key advantage is that it’s an easy substitute for diesel because it is a liquid fuel under ambient conditions making it easy to transport, store and bunker using familiar procedures. The cost of converting diesel engines to methanol dual-fuel vessels and installing the land-based infrastructure is significantly lower than other alternative fuels that require pressurization or cryogenics.
Fossil-based methanol (known as grey or brown methanol, depending on whether derived from gas or coal) burns cleaner and delivers a tank-to-wake CO2 reduction of about 7% compared to diesel but performs worse on a well-to-wake basis. However, blue or green methanol (made from renewable biomass or via an electrolysis process), while expensive and still only available in limited quantities, are chemically identical to conventional methanol, which means there are no future compatibility issues or further engine investment required by shipping companies, allowing a seamless, gradual transition to meet future well-to-wake emissions rules.
A safe transition
As a low flashpoint fuel, methanol does impose additional safety considerations in some instances e.g., during bunkering operation, which is the primary reason ABS decided to publish the first Technical Advisory on methanol bunkering providing guidance on the technical and operational challenges that must be overcome.
The main methods of methanol bunkering are truck tanker-to-ship, barge/ ship-to-ship and land storage tank-to-ship. For smaller vessels that may run on methanol fuel cells, it’s possible to provide the fuel in portable tanks.
Because of the low flashpoint and toxic properties, hoses and connections must be approved for methanol use and inspected periodically in compliance with the latest version of MSC.1-Circ. 1621. The fittings and connections should be cleaned, tight fitted, quick release and a self-sealing type. Seals are to be in good condition, pressure-tested and hoses are to be recertified according to the above IMO circular. Any mobile facilities such as tank trucks, rail cars and portable tanks should conform to meet ISO and other standards for handling methanol fuel.
For port operations, it’s important to verify compatibility, transfer rate, vapor return arrangements, communications, Emergency Shut Down (ESD), and emergency procedures. The responsibilities and procedures are to be agreed upon and confirmed in writing prior to starting bunkering – a checklist is a good way to confirm compatibility and capture this information and ABS Technical Advisory includes sample checklists to help with this work.
It’s important the receiving and supply barge if applicable are safely moored and adequately fendered, with all due attention to tidal and weather conditions not to mention surges from passing ships. Hoses should have sufficient slack to allow for any expected relative motion and the manifold arrangements, spill containment systems, and hose connections for the supply source and the receiving ship should be confirmed including emergency release (hose breakaway) arrangements.
Spark aware
Because of the low flash point, it’s important to be particularly careful about potential sources of ignition. Road truck/ISO tanks and ship should be earthed with a bonding wire to protect from static electricity. Materials should be non-sparking, the risks of electrical arcing addressed, and careful consideration needs to be given to make sure both the supply source and receiving ship don’t introduce any source of ignition into any hazardous area.
Vapor return needs to be carefully managed to ensure systems are compatible and have sufficient space, given that the estimated volume of vapor is 1: 1.4 times more than the cargo space volume it replaces. And both the supply source and receiving ship need to have inerting and purging capabilities. It’s obviously vital to have firefighting and emergency procedures in place.
Safety is rooted in good communication. There needs to be compatible communications between the supply source and the ship so both parties can monitor the bunkering operation, and, if necessary, initiate an emergency shutdown.
A ship-to-shore link is to be provided to enable automatic and manual ESD of bunkering operations. The ESD should be capable of activation from both the bunker receiving ship and the bunker supplier, and the signal should simultaneously activate the ESD on both sides of the transfer operation with no release of liquid or vapor during this procedure. An ESD might be activated for a wide range of reasons, including an overflow in receiving tank, high tank pressure, a leak, vapor or fire detection, loss of ventilation in double wall piping, excessive ship movement, abnormal pressures in the transfer system or power failure.
At the manifold connection a manually operated stop valve and a remotely operated shutdown valve are to be provided. This remote valve is to be of the fail-close type, which closes on loss of actuating power, and be capable of manual closure and to have indication of the valve position. There are multiple industry standards and regulations that apply to emergency shutdown and related safety systems, and these are listed in our Advisory, along with additional ABS recommendations. These include that systems are designed to accommodate surge pressures and that manual operation of the ESD system is possible by a single control on the bridge, safe control station and at least two strategic positions around the bunker manifold area.
The human factor
Crew training and certification are essential for safe methanol bunkering, with the minimum requirements outlined in the IGF Code and the Interim Guidelines for the Safety of Ships Using Methyl/Ethyl Alcohol as Fuel or the Seafarers’ Training, Certification and Watchkeeping (STCW) Code for IBC Code Vessels. Formal training should include basic handling, including scenarios for leakage, spillage and fire. Personnel should understand methanol’s properties, its operational risks and hazards, fire prevention and firefighting protocols, and importantly, clearly understand their roles and responsibilities, particularly in the event of an emergency. Only those with the proper training should be allowed into the designated safety zone for the bunkering operation, which is an ignition-free area with clearly defined boundaries, typically set by a risk assessment and determined by regulations.
For shipowners considering the fuel mix of their fleet, methanol passes the PACES test. It’s a proven fuel, with existing bunkering infrastructure in some ports and more being built. Making sure this bridging fuel is handled safely, particularly during bunkering, is going to be key to the ongoing displacement of fossil fuels in the global fleet. This Technical Advisory should help with this effort as the maritime industry steams towards IMO2030 and beyond.
Quaim Choudhury is Senior Managing Principal Engineer at ABS.
No comments:
Post a Comment